Our Ability to Moulding Polyurethane
We offer custom polyurethane molding services to customers for various industries. Our molded polyurethane capabilities encompass the following areas:
Ability to select and handle raw materials for polyurethane elastomers:We are familiar with the properties of different types of polyurethane materials and are able to select the right polyurethane formulation according to the product requirements, such as hardness, elasticity, abrasion resistance, chemical resistance and other different properties. And we are able to pre-treat polyurethane raw materials, such as drying, mixing and other operations to ensure stable material quality.
Mold design and manufacturing ability: We are able to design and manufacture molds according to customers' requirements or design drawings. We have our own machining workshop, including CNC machining, wire cutting, etc., to ensure the precision and quality of the molds.
Polyurethane molding process control ability: With advanced production equipment and skilled operators, we are able to accurately control the temperature, pressure, time and other parameters in the molding process, and we are able to deal with common problems in the molding process, such as air bubbles, shrinkage, deformation and so on, in order to ensure the stable quality of polyurethane products and production efficiency. Meanwhile, we master different polyurethane molding processes, such as casting polyurethane, compression molded polyurethane, injection molded polyurethane, polyurethane extrusion, etc., and are able to choose the appropriate process according to the product characteristics.
Our Polyurethane Manufacturing Process
Quality Inspection and Quality Control Ability
For each customer order, we are able to reasonably arrange the production plan, optimize the production process, improve the production efficiency, and ensure the delivery of products on time.
We have established a perfect quality inspection system, and we are able to test the appearance, size, hardness and physical properties of the molded polyurethane products to ensure that the quality of the products meets the standards.
Customer Service Capability
We provide customers with professional consultation on polyurethane molding technology, including advice on material selection, molding process, product performance and so on. We help customers understand the advantages and scope of application of polyurethane molding in order to make the best decision.
At the same time, we can provide customized polyurethane molding solutions according to customers' special needs. This may include products with special shapes, sizes, and performance requirements, as well as small-lot, multi-variety production needs.
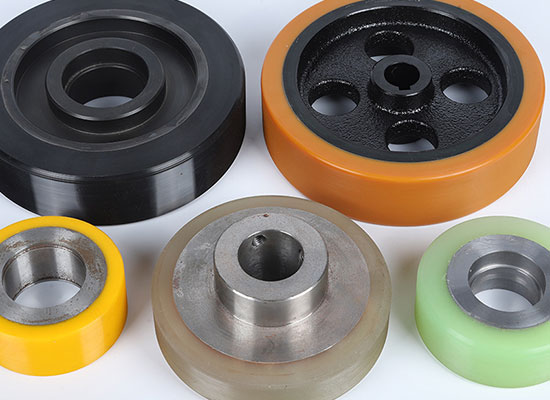
- Some Cases of Molded Polyurethane
- Step of Polyurethane Molding Process
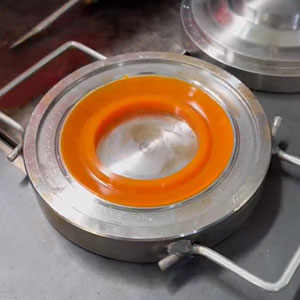
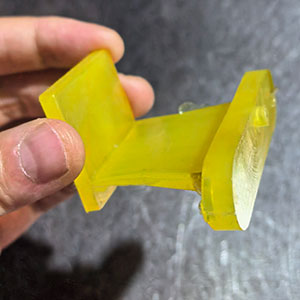
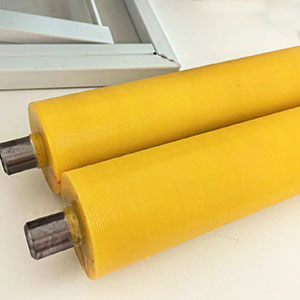
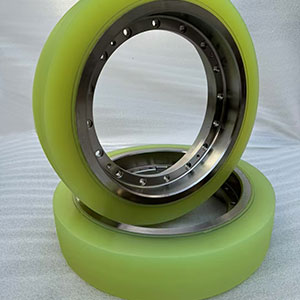
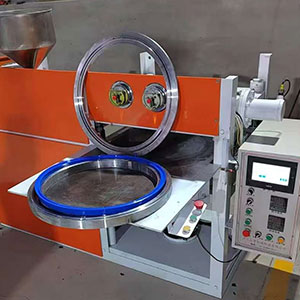
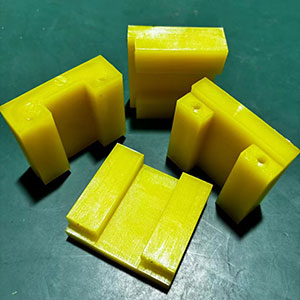
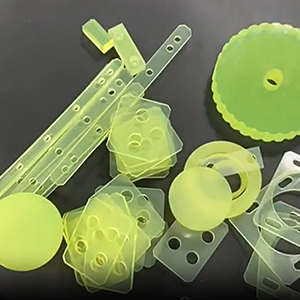
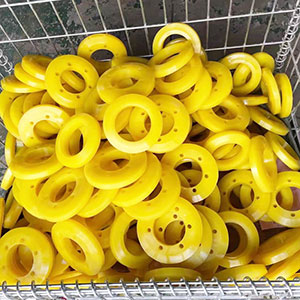
The following are common steps in the polyurethane molding process:
1. Raw material selection: according to the product performance requirements, select the appropriate polyol, isocyanate and other raw materials.
2. Formulation design: Determine the precise proportion of various raw materials and the type and dosage of additives.
3. Pre-mixing treatment: pre-mix some raw materials to ensure uniformity.
4. Measuring and mixing: accurately measure the raw materials according to the set ratio and mix them fully in the special equipment.
5. Mold Preparation: Clean the mold, apply mold release agent to ensure that the mold is intact and meets the molding requirements.
6. Pouring or Injection: The mixed material is injected into the mold.
7. Curing Reaction: The polyurethane cures under specific temperature, pressure and time conditions.
8. demolding operation: when curing is complete, the product is carefully removed from the mold.
9. Post-processing: This includes deburring, sanding, trimming, quality control, etc. to meet the final quality requirements of the product.
How to Choose the Right Polyurethane Molding Process?
When you select a suitable polyurethane molding process according to your product characteristics, several key factors need to be considered:
1. The size and shape of urethane molded parts. If they have complex shapes or are large-sized, a specific molding process might be needed.
2. The precision and surface quality of the molded polyurethane parts. If you have high demands for the precision and surface finish of the product, a precision casting process could be more appropriate.
3. Physical properties of polyurethane molded parts, such as strength, hardness, elasticity, etc. Polyurethane products made by different processes may vary in these properties.
4. For mass production, processes with a high degree of automation, such as injection molding, may be more cost-effective. For small lot or single piece production, hand pouring or reaction injection molding may be more flexible.
5. Molding Process characteristics. For example, polyurethane pouring is suitable for simple shapes, large or thick-walled products, but its productivity is relatively low. Injection molding enables high precision, complex shapes, and high productivity, but the mold costs are higher. Reaction injection molding is suitable for large, thin-walled and complex shapes, and it has shorter production cycles.
6. Cost budgeting including:
- Molds costs: the cost of molds varies from process to process and needs to be considered.
- material costs: The prices of polyurethane raw materials for different formulas are different, such as TDI, MDI, NDI, PPDI etc.
- Production efficiency: polyurethane elastomers with different properties have varying degrees of processing difficulty, the time efficiency of production also varies.
Consider all of these factors to select the best polyurethane molding process for your project.
Advantages of Polyurethane Molding
1. Diversified Performance: Diversity of properties: Polyurethane formulations can be adapted to specific needs in order to obtain different hardness, elasticity, abrasion resistance, chemical resistance and physical properties, thus adapting to a wide range of application scenarios.
2. Easy Processing: Molded urethane products can be produced by injection molding, extrusion molding, casting molding, compression molding, centrifugal casting molding, rotational casting molding, etc.
3. Good Bonding Properties: Good adhesive properties with a variety of materials and substrates, easy to manufacture composite structure products
4. High Cost-effectiveness: In mass production, can effectively control costs, while maintaining good product quality.
We can produce molded urethane products in a variety of shapes and sizes, including but not limited to rollers & wheels, buffer, shock absorber, pads, bushings and motor mounts, die springs, spacer, washers, gasket, liners, sheet, rods etc. PU parts, to meet your specific needs.
Of course, our professional team can work with you to provide design suggestions and solutions based on your needs or design drawings.
Depending on the specific product and production process, our MOQ usually ranges from tens, hundreds to thousand pieces.
Generally speaking, the production lead time is about 2-6 weeks, but it will vary depending on the complexity and quantity of the order.
Prices are mainly calculated based on product specifications, materials, process complexity and order quantity.it's better if you can provide the drawing.
Before finalizing the mass production, we can provide you with samples so that you can evaluate whether the product meets your requirements.