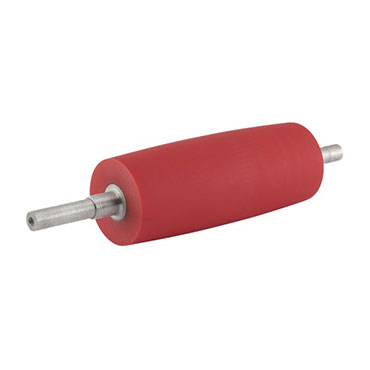
Polyurethane Drive Rollers
Polyurethane drive rollers are the core components of power transmission in industrial conveyor systems. Through close contact with the conveyor belt, it relies on friction to transfer the rotary motion of the motor and other power sources to the conveyor belt, so that the conveyor belt can run continuously and stably, and realize the efficient conveying of materials. Polyurethane drive rollers are capable of precise transmission, increased friction, cushioning protection, and a variety of different industrial conveying conditions.
Custom Urethane Drive Roller Manufacturer
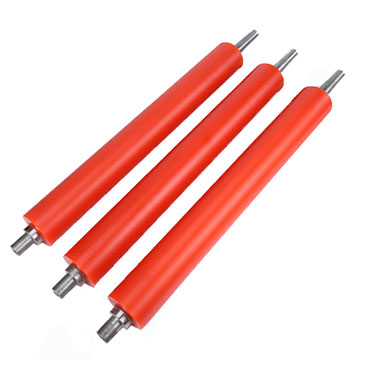
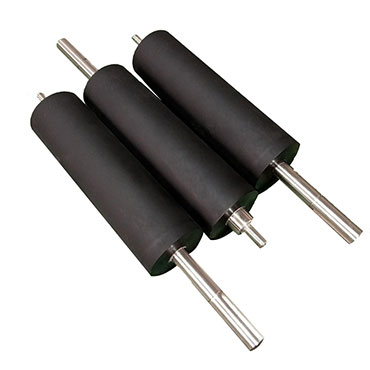
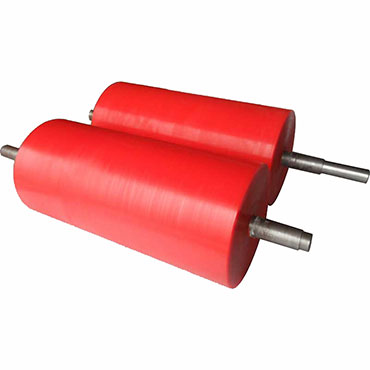
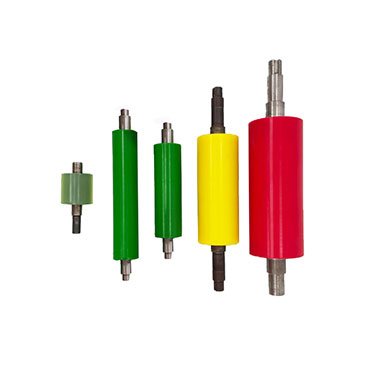
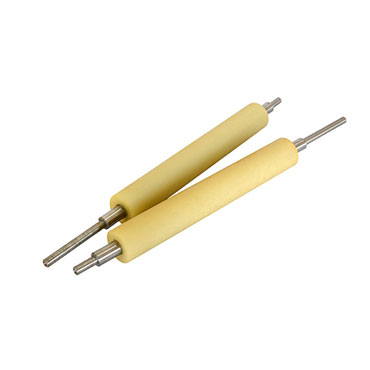
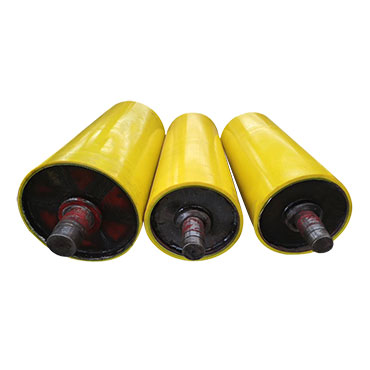
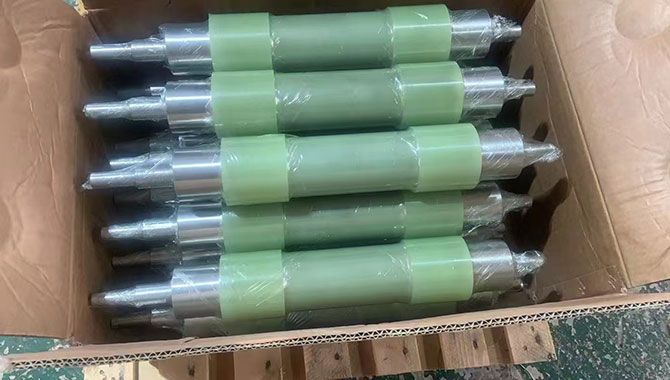
Urethane Drive Roller Performance Advantages
Polyurethane drive rollers have excellent abrasion resistance, reducing the frequency of replacement and lowering maintenance costs; anti-aging and chemical resistance; good friction, effectively preventing the phenomenon of slipping and improving the reliability of the conveyor system; and can be customized and optimized rollers structural design, so that the polyurethane drive rollers are able to meet the individual needs of customers.Our Custom Polyurethane Drive Rollers Capability
- 1. we can select the suitable formula of polyurethane materials according to your different application scenarios and performance requirements, and adjust the formula of polyurethane materials to meet the special requirements of customers on the performance of drive rollers.
- 2. We can design and manufacture molds according to the parameters provided by customers (such as size, shape, hardness, quantity required and other requirements).
- 3. We master a variety of polyurethane molding processes, such as casting molding, injection molding, compression molding. Different molding processes are suitable for different types and specifications of drive rollers, you can choose the appropriate process according to the characteristics of urethane drive rollers.
- 4. We are equipped with advanced processing equipment, such as CNC lathes, milling machines, grinding machines, etc., for processing the core and body of the drive rolls. Various surface treatments can also be applied to the surface of polyurethane drive rolls to meet the different needs of customers for the surface characteristics of drive rollers.
- 5. Quality control ability, in the production process, we establish a strict quality control system, real-time monitoring and inspection of each production link. From raw material procurement inspection, parts processing process inspection to final inspection of finished products, we check at all levels to detect and solve quality problems in a timely manner to ensure that every customized polyurethane drive roller meets the customer's quality requirements.
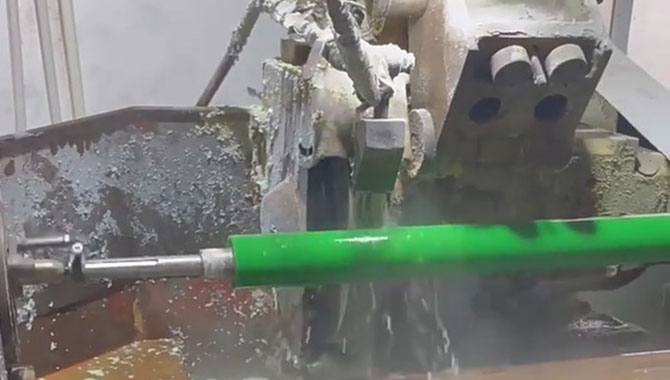
Classification by Polyurethane Drive Rollers Characteristics
- Product Specifications
- Gallery
Polyurethane Drive Rollers VS Rubber or Metal Drive Rollers
- 1. Excellent wear resistance
- 2. Good friction
- 3. Anti-aging and chemical resistance
- 4. Design flexibility and customization
- 5. Cushioning properties
1) Compared with rubber drive rollers, polyurethane material has higher hardness and strength, and its wear resistance is superior. In the process of long-term contact and friction with the conveyor belt, the polyurethane drive roller wears slower, and can maintain good performance in a long time of operation, reducing the size change and performance degradation of the drive roller due to wear and tear, thus reducing the frequency of replacement and maintenance costs.
2) Compared with metal drive rollers, metal drive rollers are prone to wear and scratches in some friction and impact environments, while polyurethane drive rollers have good anti-wear ability, which can ensure power transmission while extending its own service life and improving the overall operating efficiency of the equipment.
1) The surface characteristics of polyurethane material can provide stable and large friction, compared with some plastic drive rollers, the friction between polyurethane drive rollers and conveyor belts can better meet the transmission requirements in actual work. This good friction can effectively prevent the conveyor belt from slipping during operation, ensure the stable operation of the conveying system, and improve the conveying efficiency and reliability.
1) Compared with rubber drive rollers, polyurethane drive rollers have better anti-aging performance. Rubber is easily affected by ultraviolet rays, oxygen, temperature and other environmental factors and aging, hardening, brittleness and other phenomena, thus affecting the performance and life of the drive roller. The polyurethane material has a stronger resistance to environmental factors, and can maintain relatively stable performance under different climatic conditions and environments, and is less likely to show obvious performance deterioration in long-term use.
2) In terms of chemical resistance, polyurethane drive rollers can withstand the erosion of a variety of chemical substances. Compared with ordinary metal drive rollers, which are easily corroded by chemical substances, polyurethane drive rollers, after special treatment, can work normally in environments where there is a risk of chemical corrosion, such as conveyor systems in the chemical industry, electroplating and other industries.
Polyurethane materials can be made into drive rollers of various hardnesses, shapes and sizes through different formulations and processing techniques to meet the special needs of different users. Compared with some traditional materials, drive rollers have a greater advantage in customization. Whether it is special size, special surface treatment or special functional requirements, polyurethane drive rollers can better achieve customized production and provide users with personalized solutions.
Compared to metal and some rigid plastic drive rollers, polyurethane drive rollers have a certain degree of elasticity that provides a cushioning effect during operation. This reduces the impact between the conveyor belt and the drive rollers, reduces the wear and tear of the conveyor belt, and extends the service life of the conveyor belt. At the same time, the cushioning effect can also reduce the vibration and noise during the operation of the equipment, creating more favorable conditions for the production environment.
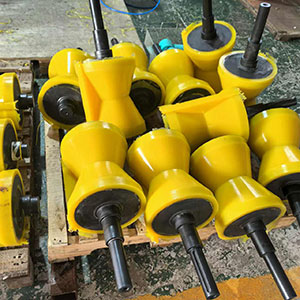
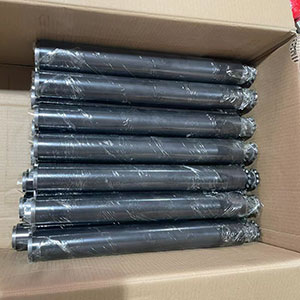
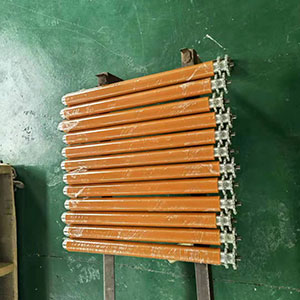
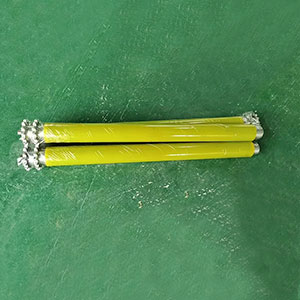
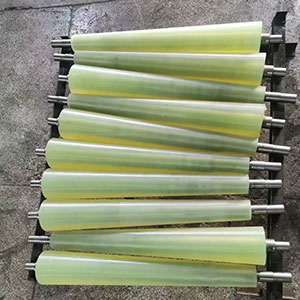
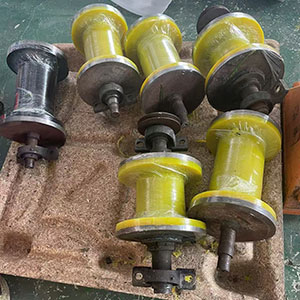
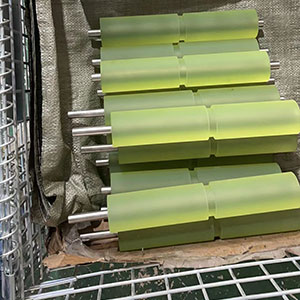
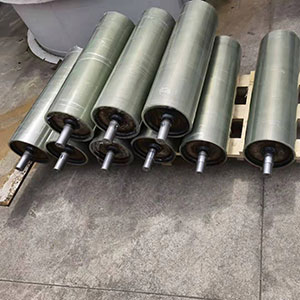
Related Products
What is polyurethane drive roller application scenario?
- 1. Manufacturing
- 2. Food and beverage industry
- 3. Logistics and warehousing industry
- 4. Mining and Energy Industry
- 5. Paper and printing industry
1) Automobile manufacturing: In the automobile production line, polyurethane drive rollers are used for conveying automobile parts, car bodies, etc. The precise transmission performance ensures that the parts can be accurately conveyed to various processing and assembly stations. Its precise transmission performance ensures that the parts can be accurately transported to the various processing and assembly stations, improving production efficiency and product quality.
2) Electronics Manufacturing: The electronics manufacturing industry requires a high degree of precision in its products. Polyurethane drive rollers can ensure the positional accuracy and conveying speed stability when conveying electronic components and circuit boards, preventing components from being damaged during the conveying process and ensuring the production quality of electronic products.
1) Food processing: Food production process requires strict hygiene. Polyurethane materials comply with food hygiene standards, non-toxic, tasteless, and not easy to breed bacteria. Therefore, polyurethane drive rollers are widely used in food processing production lines, such as bread, meat, fruits and other food transportation, which can ensure the safety and hygiene of food, but also meet the needs of efficient production.
2) Beverage Filling: In beverage filling lines, polyurethane drive rollers are responsible for conveying bottles, cans and other packaging containers. Its good friction and stable transmission performance ensures that the containers will not shake or fall during the conveying process, which ensures that the filling process is carried out smoothly.
1) Automated warehousing system: In modern logistics warehouses, automated conveying system is the key to improve the efficiency of warehousing. Polyurethane drive roller as an important part of the conveyor equipment, can realize the fast and accurate delivery of goods, whether it is a small parcel or large goods, through the drive roller and conveyor belt with the efficient completion of the handling and storage tasks.
2) Sorting system: Logistics sorting centers need to sort a large number of goods according to different destinations. Polyurethane drive rollers can accurately control the running speed and direction of the conveyor belt, so that the goods accurately arrive at the corresponding sorting port, greatly improving the sorting efficiency and accuracy.
1) Coal Mining and Transportation: In the coal conveying system of underground and surface coal mines, polyurethane drive rollers can run stably for a long time and convey a large amount of coal by virtue of their high abrasion-resistant and strong load-bearing capacity. The continuity of coal conveying can be guaranteed even in harsh working environments, such as high dust and humid mines.
(2) Ore processing: During the mining and processing of metal ores, it is necessary to convey the ores from the mining place to the processing plant for crushing, screening and other treatments. Polyurethane drive rollers can adapt to the weight and hardness of the ores, ensuring that the entire conveying process is carried out efficiently, providing strong support for the production of ore processing.
1) Paper production: In the production line of a paper mill, the polyurethane drive roll plays an important role from the transportation of pulp to the winding of the finished paper. It is able to maintain good performance in humid environments, accurately controlling the conveying speed and tension of the paper to ensure the quality of the paper and the continuity of production.
2) Printing Lines: The printing process requires that the paper be transported to the printing stations accurately and without error. The precise transmission performance of polyurethane drive rollers can ensure the positioning accuracy of paper in the conveying process, so that the printing pattern is accurate and clear, and the printing quality is improved.
First you need to provide us with detailed product requirements, including size, performance, application scenarios and other information. Our sales and technical team will evaluate and give a preliminary proposal and quotation. After both parties confirm and sign the contract, we start to arrange the production. There will be strict quality inspection during the production process, and the products will be delivered as agreed upon upon completion.
It depends on the complexity of the product and the number of orders. Generally for simple specifications, the production cycle is 2-4 weeks; for complex customization, it may take longer, we will give you the exact time according to the specific situation when you inquire.
We are currently able to produce rolls with a maximum outside diameter of 500 mm and a maximum length of 4 meters, and a minimum outside diameter of 10 mm. However, the exact size range will vary depending on product performance requirements and other factors.
The durometer range is typically between 85 - 90 Shore A. The lower durometer (Shore A) is the highest. Lower hardness (50 - 70 Shore A) drive rolls are used for cushioning and gentle conveying, e.g. electronic component conveying, while higher hardness (50 - 80 Shore D) drive rolls are used for high loads and high precision drives, e.g. automotive manufacturing lines.
Within 3 months, if the product fails due to quality problems, we will provide repair or replacement service. Outside the warranty period, we will also provide technical support and charge a reasonable maintenance cost. Our after-sales team will respond within 24 hours after receiving feedback.