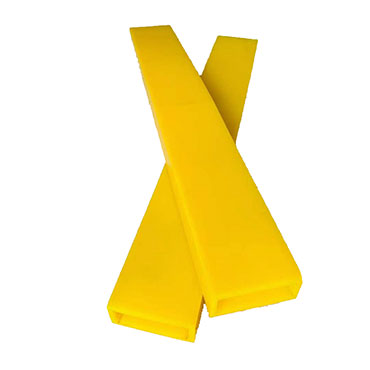
Polyurethane Fork Covers
Polyurethane fork covers, also called polyurethane forklift fork covers, is a kind of protective device installed in the fork tines of forklift trucks. It is mainly used to protect the fork tines of forklift trucks from all kinds of damages during daily operation, and at the same time, it can also enhance the safety and stability of operation to a certain extent.
This kind of protective sleeve closely fits with the forklift tines and acts as a cushion and protective layer between the forklift tines and the objects in contact with the goods, shelves and the ground when the forklift is picking up and carrying the goods.
Custom Polyurethane Forklift Fork Covers & Protectors
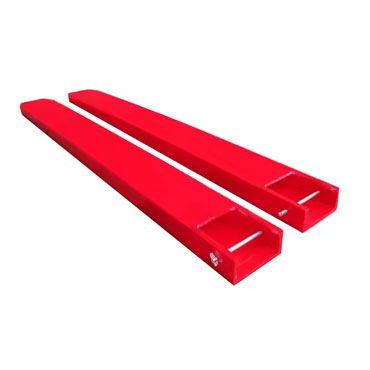
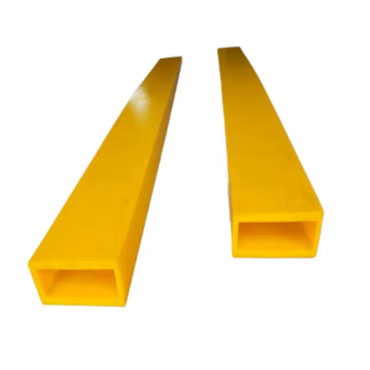
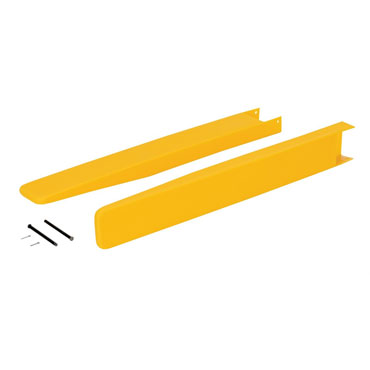
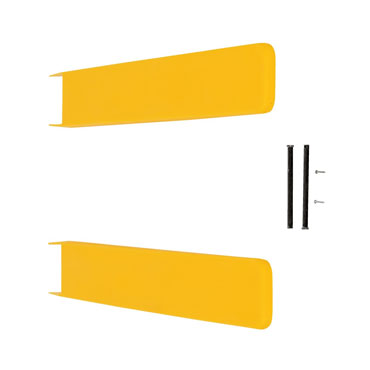
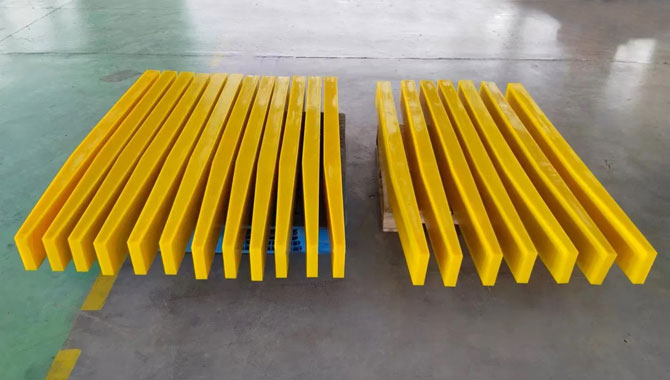
Advantage of Polyurethane Fork Covers
- Excellent abrasion resistance, corrosion Resistance and impact resistance;
- Good weather resistance and Waterproof;
- Precise fit and convenient installation;
- Appearance design and Personalization options;
Application of Urethane Forklift Fork Sleeve
Polyurethane forklift sleeves are suitable for all types of forklifts, mechanical equipment or working scenarios. Whether it is an electric forklift, fuel forklift, pallet trucks, pallet stackers and trailers, or in a variety of operating environments such as logistics warehouses, construction sites, port terminals and so on. our polyurethane forklift sleeves can be perfectly adapted to play an excellent protective role.
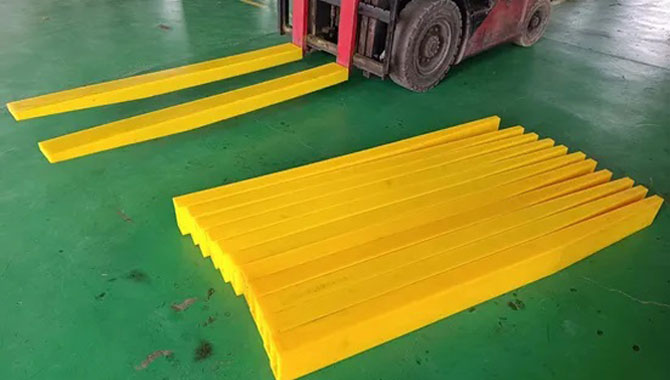
Custom Molded Urethane Fork Sleeves
- Product Specifications
- Gallery
Polyurethane fork covers fit a wide range of fork types, preventing scratches and punctures from rough fork surfaces and sharp fork tips. They are made of highly abrasion-resistant polyurethane elastomer material, and the size can be customized according to your fork length, width, and thickness.
Polyurethane forklift fork covers have high compressive strength, good resilience, are lightweight and flexible, and are easy to remove and install, which can greatly reduce forklift collisions with cargo and provide a quieter, more comfortable forklift environment.
Specification of Polyurethane Fork Covers
common forklift fork size | ||||||||||
LxWxT | W | T | L | Forklift | ||||||
mm | mm | mm | mm | |||||||
920x100x30 | 100 | 30 | 920 | 1070 | 1220 | 1370 | 1520 | 1t | ||
920x100x35 | 100 | 35 | 920 | 1070 | 1220 | 1370 | 1520 | 1.5t | ||
1070x120x40 | 120 | 0 | 1070 | 1220 | 1370 | 1520 | 1670 | 1820 | 1970 | 2t |
1070x120x45 | 120 | 45 | 1070 | 1220 | 1370 | 1520 | 1670 | 1820 | 1970 | 2.5t |
1070x125x45 | 125 | 45 | 1070 | 1220 | 1370 | 1520 | 1670 | 1820 | 1970 | 3t |
1070x125x50 | 125 | 50 | 1070 | 1220 | 1370 | 1520 | 1670 | 1820 | 1970 | 3.5t |
1070x125x50 | 125 | 50 | 1070 | 1220 | 1370 | 1520 | 1670 | 1820 | 1970 | 4t |
1070x150x50 | 150 | 50 | 1070 | 1220 | 1370 | 1520 | 1670 | 1820 | 1970 | 4.5t |
1220x150x50 | 150 | 50 | 1220 | 1370 | 1520 | 1670 | 1820 | 1970 | 2120 | 5t |
1220x150x60 | 150 | 60 | 1220 | 1370 | 1520 | 1670 | 1820 | 1970 | 2120 | 6t |
1220x150x65 | 150 | 65 | 1220 | 1370 | 1520 | 1670 | 1820 | 1970 | 2120 | 7t |
1220x170x70 | 170 | 70 | 1220 | 1370 | 1520 | 1670 | 1820 | 1970 | 2120 | 8t |
1220x175x80 | 175 | 80 | 1220 | 1370 | 1520 | 1670 | 1820 | 1970 | 2120 | 10t |
1220x150x50 | 150 | 50 | 1220 | 1370 | 1520 | 1670 | 2270 | 2420 | 2570 | 5t |
1220x150x60 | 150 | 60 | 1220 | 1370 | 1520 | 1670 | 2270 | 2420 | 2570 | 6t |
1220x150x65 | 150 | 65 | 1220 | 1370 | 1520 | 1670 | 2270 | 2420 | 2570 | 7t |
1220x170x70 | 170 | 70 | 1220 | 1370 | 1520 | 1670 | 2270 | 2420 | 2570 | 8t |
1220x175x80 | 175 | 80 | 1220 | 1370 | 1520 | 1670 | 2270 | 2420 | 2570 | 10t |
Date Sheet of Polyurethane Elastomer Physical Property
Polyurethane Prepolymer Properties | |
% NCO | 4.3±0.2 |
Appearance@20℃ | Transparent liquid |
Viscosity@80℃/mPa·s | 800 |
Melting condition,h/°C,20L | 8/80 |
Curing agent | MOCA |
Chain expansion coefficient(NH2/NCO) | 0.9 |
Amount of curing agent(per 100 parts of prepolymer) | 12.5 |
Temperature of prepolymer/°C | 80 |
Curing agent temperature/°C | 110 |
Recommended mold temperature/°C | 100 |
Gel time/min(400g mix) | 6~8 |
Demolding time/min(400g mix) | 30~40 |
Post-curing,h@℃ | 16/100 |
Hardness@20℃,Shore A | 85±2 |
Hardness@20℃,Shore D | - |
Tensile strength/MPa | 28.6 |
100% constant tensile strength/MPa | 7.6 |
300% constant tensile strength/MPa | 11.2 |
Elongation at break/% | 520 |
Tear Strength/(Right Angle,KN/m) | 80 |
Resilience/% | 32 |
DIN roller abrasion/m㎡ | 162 |
Application Scenarios of Polyurethane Forklift Cover
- Mechanical industry: When transporting valuable mechanical equipment and mechanical parts, the use of polyurethane forklift covers can avoid the wear and tear of the equipment and parts, and protect the surface and precision of the precision parts.
- Iron and steel industry: When transporting all kinds of metal coils and plates by forklift, it can prevent the forklift from damaging the surface of plates and maintain the surface quality of metal plates.
- Construction industry: When transporting bricks, stones, glass and other building materials, it can avoid the wear and tear of building materials and reduce the loss of materials.
- Logistics industry: When transporting all kinds of goods, it can reduce the damage of goods and improve the quality of transportation and storage, applicable to logistics warehouses, distribution centers and other places.
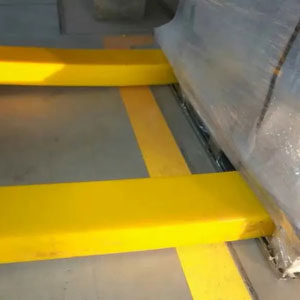
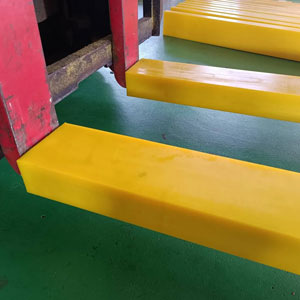
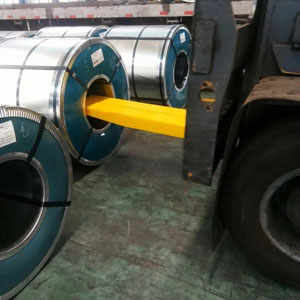
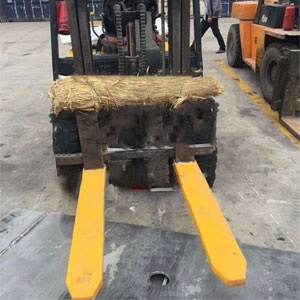
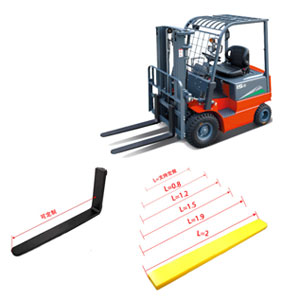
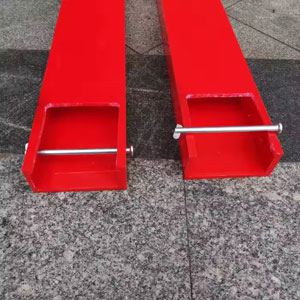
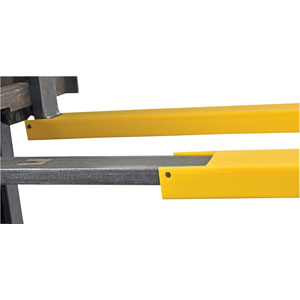
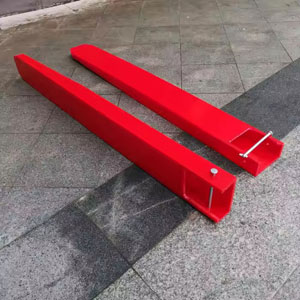
Related Products
Polyurethane Forklift Fork Covers and Protector-Urethane Casting Manufacturer
Stop letting forklift fork wear and tear affect your productivity and cost control ! Choose our Polyurethane Fork Covers for long-lasting power for your equipment. Contact us for custom polyurethane fork cover with efficient, cost-effective operations!
We offer a wide range of standard sizes of polyurethane fork bushes, covering most of the common industrial equipment forklift sizes. Meanwhile, we also provide customized service, if your forklift has special specifications, please provide the detailed size information, we can customize the suitable fork covers for you.
Absolutely. Polyurethane has excellent abrasion and impact resistance and is able to withstand the friction and impact of frequent handling of goods in a logistics and warehousing environment. After rigorous testing, our fork bushing can also maintain a long service life under high intensity use, effectively protecting the forklift forks.
The production cycle of customized polyurethane fork bushing depends on the complexity of the product and the number of orders. Generally speaking, the production lead time for a simple customized fork bushing is around [15] business days; for more complex customization needs, the production lead time may be extended to [25] working days. We will communicate with you as soon as we receive your order to confirm the exact production lead time.
Polyurethane fork bushing has many advantages over other materials. It has better abrasion resistance, which significantly extends its service life; strong corrosion resistance, which allows it to be used in harsh environments; and good impact resistance and flexibility, which better protects the fork. In addition, polyurethane fork sleeves are waterproof and weather resistant, and can be adapted to a variety of different working environments.
The price of polyurethane fork bushing mainly depends on factors such as specification size, customization requirements and order quantity. The price of standard fork bushing is relatively fixed, while customized fork bushing will be priced according to the specific difficulty of customization and material usage. You can provide us with detailed requirements and we will provide you with an accurate quotation.