Urethane Injection Molding
Our polyurethane injection molding technology and capabilities ensure that we produce parts with high dimensional accuracy and tight tolerance ranges for rapid mass production. The injection molding process produces parts with smooth, flat surfaces and good cosmetic quality, often without much subsequent surface preparation. If your parts have internal grooves, thin walls or complex geometries, then our custom polyurethane injection molding services are ideal for you.
Compared to cast urethane parts, injection molded urethane parts typically have higher stiffness and tensile strength, and deform relatively little when subjected to pressures and loads, making them suitable for structural components that are subjected to large external forces. Moreover, the molecular structure of injection-molded polyurethane parts is relatively compact, and the chemical resistance is better than that of cast polyurethane.
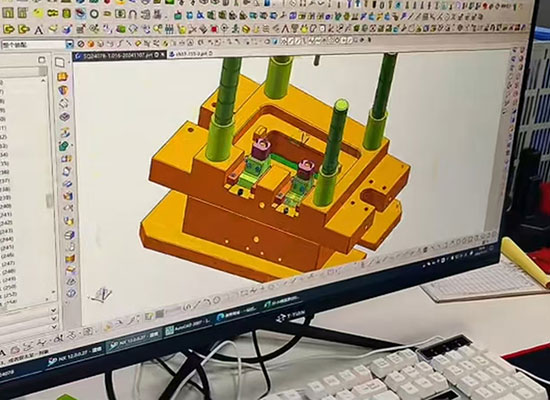
Injection Molded Polyurethane Capabilities
We are able to produce polyurethane parts with a hardness range of 70A - 98A, with high precision in product dimensions, complex shapes and small tolerances.- Polyurethane material selection
- Mold design and manufacturing capacity
- Mass production capacity
Advantage of Urethane Injection Molding
Injected polyurethane wheels, polyurethane bearings and PU parts have the following characteristics- Good abrasion resistance
- Oil and chemical resistance
- High mechanical strength
- Good elasticity and resilience
- Low compression permanent deformation
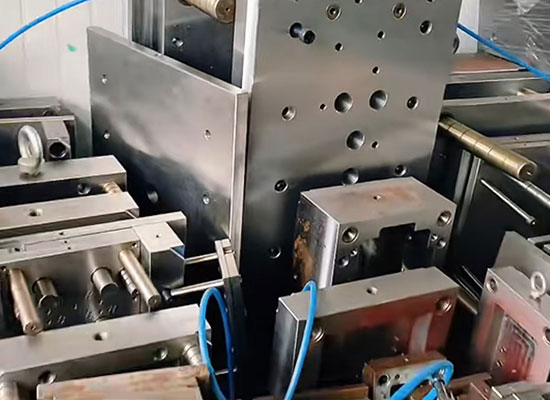
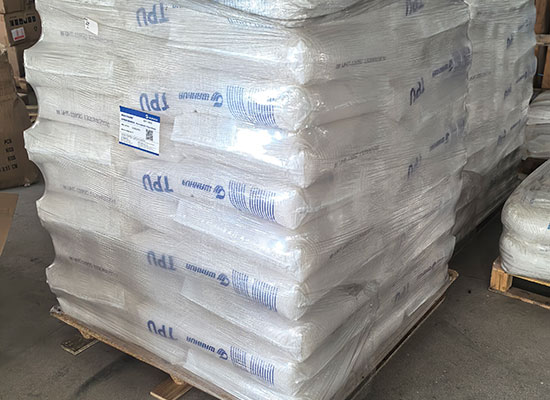
Quality Control of Injection Urethane Molding
Quality control of injection urethane molding is crucial to ensure the production of high-quality urethane products. Here are some key aspects of quality control in injection urethane molding:- 1. Raw Material and Mold Inspection
- 2. Injection Process Control, Monitor the injection pressure, temperature, and speed to ensure consistent filling of the mold. Fluctuations in these parameters can lead to defects such as voids, sink marks, or incomplete filling.
- 3. Measure the dimensions of the parts using calipers tools to ensure they meet the design specifications. Visual inspections of the molded parts for surface defects such as scratches, blemishes, or flash.
- 4. Products that are detected as non-conforming are scrapped. We have production records that can be traced back to quickly identify problems and adjust and optimize production schedules to reduce rework and increase productivity.
Cases of Injected Polyurethane Products

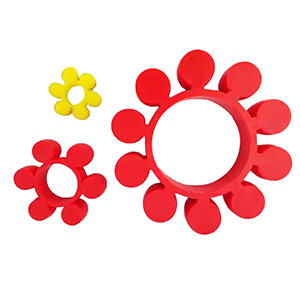
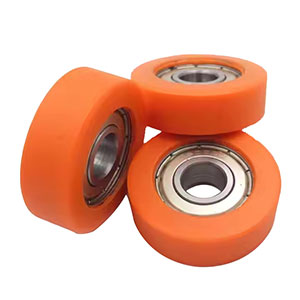
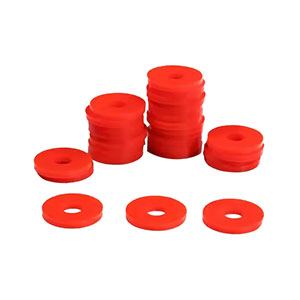
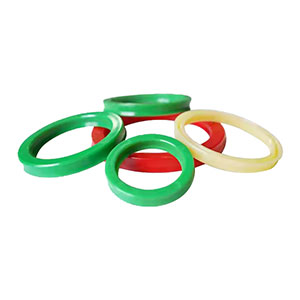
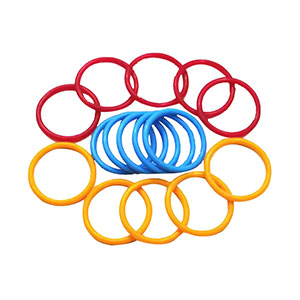
Application of Polyurethane Injection Molding
Urethane Injection Molding Parts
Polyurethane injection molding is ideally suited for high-volume, high appearance polyurethane parts production projects. Urethane molded products made by injection molding are characterized by a beautiful appearance, smooth surface and precise dimensions. But the cost of high-precision injection molding molds is relatively high.
Injection molds are usually top and bottom structures, consisting of two or more parts in a closed mold. We usually perform precision machining on the contact surfaces of the closed parts to ensure a tight fit during closure and to prevent leakage of raw materials. This ensures that the products produced are dimensionally accurate, have a complete shape and good surface quality.
Our custom polyurethane injection molding services provide you with unmatched flexibility and reliability. Our product managers assist customers in the early stages of product design and development, providing technical advice to optimize product performance and manufacturing feasibility. We can choose to manufacture simple or high-precision molds based on your production volume, budget, and the shape and specifications of the product on your drawing.
Urethane Injection Process
Polyurethane injection molding is the process of injecting molten thermoplastic polyurethane pellets under high pressure into a mold cavity where it cools and hardens.
- 1. Mold preparation
- 2.The heated polyurethane material is injected into the mold cavity through the injection molding machine.
- 3.After the injection is completed, a certain pressure is maintained to further compact the material and compensate for material shrinkage.
- 4.Through the cooling channels in the mold, the injected polyurethane is rapidly cooled and cured to form the desired shape.
- 5.After the product is fully cooled and cured, open the mold and eject the product from the mold.
We can produce urethane molded parts with Injection volume from 100 grams up to 5 kilograms. Hardness range 70A-98A from small precision parts to large industrial parts according to your specific requirements.
The production cycle depends on the complexity of the product and the quantity of the order. Generally, it is about 2-6 weeks.
Our minimum order quantity varies depending on the product type and production process. Usually, it is 100pcs.
Yes. we can provide you with samples after determining the specific customization requirements and related costs.
The price mainly depends on product size, complexity of shape, material cost, and order quantity. We will provide you with a detailed quotation.
If there is any problem with the quality of the products, we provide warranty service for a certain period of time and solve the problem for you in time.