Polyurethane Products for OEM and Automated Manufacturing
Polyurethane products play a vital role in both OEM and automated manufacturing. Their ability to be customized, durability, and compatibility with advanced manufacturing techniques make them an essential choice for manufacturers looking to optimize their production processes and deliver high – quality products. Whether it’s enhancing the performance of OEM – made equipment or enabling seamless automation, polyurethane have become indispensable materials in the manufacturing industry.
Polyurethane has both the high elasticity of rubber and the high hardness and strength of plastic, with excellent abrasion resistance (3-10 times that of general rubber), in addition, it also has good mechanical strength, flexural resistance, oil resistance, chemical resistance and excellent noise and vibration damping properties. With the continuous improvement of the technical level of the polyurethane industry, polyurethane products are gradually realizing substitution in the application fields of rubber and plastic.
Urethane OEM Replacement Parts
Polyurethane in OEM Manufacturing - Polyurethane parts are often customized to meet specific equipment requirements. For example, polyurethane gaskets can be precisely molded to fit the exact dimensions of machinery parts. This ensures a perfect seal, protecting the equipment from dust, moisture, and leaks. These gaskets are designed according to the OEM's detailed specifications, whether it's for a small consumer appliance or a large industrial machine.
Conveyor Systems- Polyurethane Rollers and Belts are a common sight in conveyor systems. They offer several advantages over traditional materials. Polyurethane has a low coefficient of friction, which reduces energy consumption and allows for smooth movement of products along the conveyor. Additionally, it is highly resistant to wear and tear, ensuring a long service life.
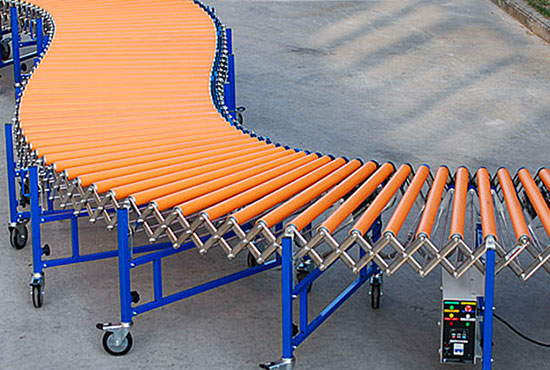
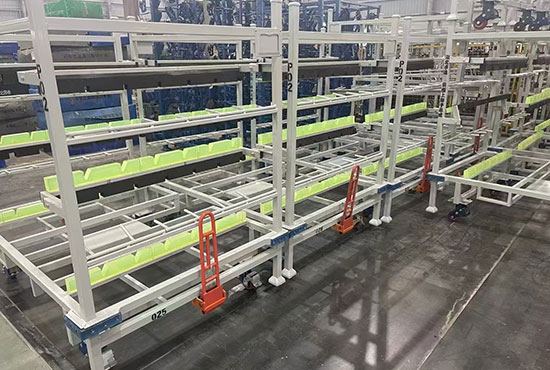
Polyurethane in Automated Manufacturing
Robotic End-Effectors- Polyurethane Grippers has high elasticity and customizable surface properties enable it to securely grasp a wide range of objects, from delicate electronic components to heavy industrial parts. For example, in the automotive industry, polyurethane coated grippers are used to handle car parts during assembly, providing a firm hold without damaging the surface. In addition to grippers, polyurethane is used to create tool attachments for robotic arms. These attachments can be designed to perform tasks such as painting, sanding, or dispensing adhesives. flexibility polyurethane parts ensuring consistent in automated manufacturing processes.
Fixtures and Jigs in Custom Molded Solutions- automated manufacturing often requires custom - designed fixtures and jigs to hold workpieces in place during machining, assembly, or inspection processes. Polyurethane can be easily molded into complex shapes to create these fixtures. It provides a stable and secure hold for the parts, while also being lightweight enough not to impede the movement of automated machinery. For example, in a precision machining operation, a polyurethane fixture can be used to hold a small, intricate part in the exact position required for accurate cutting, drilling, or milling.
Advantages of Polyurethane Productsin Automated Manufacturing
Precision Manufacturing -Polyurethane products can be manufactured with extremely high precision. Advanced polyurethane molding techniques allow for tight tolerances, ensuring that each component fits exactly as required in automated systems. This precision is essential for maintaining the accuracy and consistency of automated manufacturing processes.
Durability and Longevity-Automated manufacturing often involves continuous operation, and components need to withstand significant wear and tear. Polyurethane products are known for their durability, with high resistance to abrasion, chemicals, and mechanical stress. This means that they can last longer in demanding automated manufacturing environments, reducing the frequency of replacements and associated downtime.
Design Flexibility- The material can be formulated and molded into a wide variety of shapes, sizes, and hardness levels. This design flexibility allows manufacturers to create custom - tailored polyurethane products that meet the specific needs of their automated manufacturing processes. Whether it's a complex geometric shape or a component with unique mechanical properties, polyurethane can be engineered to fit the requirements.
Lightweight yet Strong-Polyurethane products offer a favorable strength - to - weight ratio. This is beneficial in automated manufacturing, as lightweight components can reduce the overall weight of robotic systems and moving parts, leading to faster and more energy - efficient operation. At the same time, polyurethane's strength ensures that it can handle the necessary loads and forces in manufacturing processes.
Pulisen has been in the custom polyurethane molding business for over 10 years. It is this experience that allows us to understand, anticipate and respond to the customized needs of our diverse customers. Our process is flexible. We can start with your drawings, designs or sketches. No matter where you are in the production process, we will provide high quality cast urethane products and the right urethane solution for original equipment manufacturers (OEMs) and automated manufacturing!
Explore other Industries Service
Send Inquiry
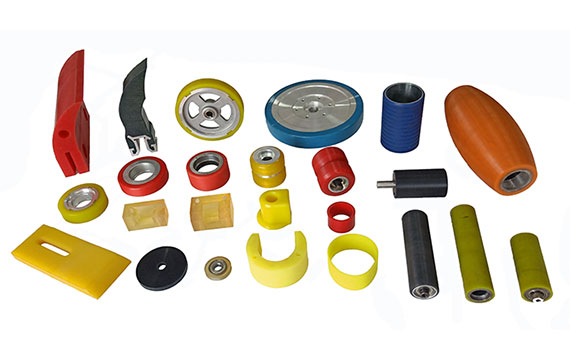